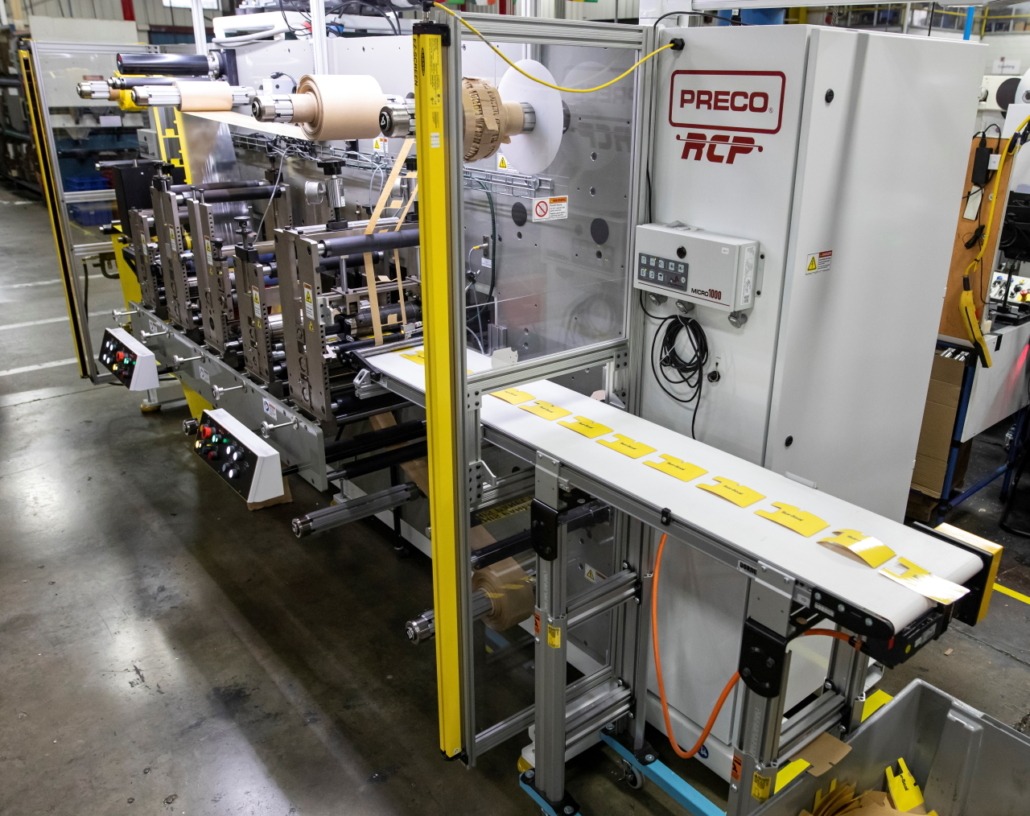
At Sur-Seal, we pride ourselves on offering innovative material solutions designed to meet diverse customer needs. Our proprietary products, including...
Skiving is a manufacturing process that precisely shaves thin layers of materials to achieve the desired thickness and surface quality. This technique is particularly valuable in industries where component accuracy is non-negotiable, such as aerospace, automotive, and high-performance electronics.
With the integration of computer-aided design (CAD) and computer-aided manufacturing (CAM), skiving delivers the precision and control needed to meet strict tolerance requirements.
Whether you’re a cross-functional engineer or part of a procurement team, understanding the advantages of skiving can inform material choices and reduce project costs.
In this article, we explore the benefits of skiving, from boosting efficiency and precision to enhancing scalability and product aesthetics.
Skiving is more than a simple method of material reduction; it’s a precision process that can significantly improve product reliability and performance across applications.
Here’s why skiving matters:
Sur-Seal leverages skiving technology and automation to help clients adapt to fluctuating order volumes and evolving material needs. This adaptability enables us to support growth across diverse industries, providing scalable solutions that reduce costs and enhance product quality.
Sur-Seal’s recent addition of a state-of-the-art skiving machine brings the precision and efficiency required to reduce material thickness, enhance product quality, and lower production costs.
Here are some of the ways we can help:
Sur-Seal combines cutting-edge skiving technology with a full suite of support services to provide end-to-end solutions for our clients.
Collaborating closely with industry leaders like 3M, we offer rapid prototyping to ensure quick, effective solutions tailored to your needs.
Our goal is to build long-term partnerships with our clients so that we can help you maximize savings and efficiency over time. From material selection to streamlining your production process, Sur-Seal offers comprehensive support at every stage of the design and manufacturing process.
Skiving’s accuracy, efficiency, and adaptability make it a powerful tool in today’s competitive manufacturing landscape. It allows businesses to meet rigorous standards and achieve long-term success.
Sur-Seal offers a high-performance solution that benefits a range of industries, from aerospace to electronics. It produces smooth, accurate surfaces that meet the most demanding specifications.
Partner with Sur-Seal to leverage the advantages of precision skiving for cost savings without compromising quality. Contact Sur-Seal today to learn more about how our skiving capabilities can give your business a competitive edge.