Top-Rated Die-Cutting Services With Sur-Seal
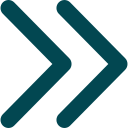
Fast, Affordable Prototyping

Aerospace Grade at Industrial Prices
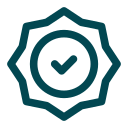
Clean Room Capabilities
Die-cutting is one of the best ways for businesses to create functional parts for their products without needing to use expensive materials. Rather than using metallic substances to create working parts, die-cutting combines more malleable materials to create precise, finished parts quickly and at a more affordable cost. Sur-Seal’s die-cutting and manufacturing services have created thousands of parts for companies of all sizes — from Fortune 500 to local entrepreneurs.
Call 513-574-8500 or contact Sur-Seal online for more information about our die-cutting services.
Types of Die-Cutting Services With Sur-Seal
Sur-Seal offers two types of custom die-cutting services to those seeking to rapidly produce high-quality parts for a lower cost. Each has their own set of benefits and are best used for different order types.
For flatbed die-cutting, rotary die-cutting, or other die-cutting services, call 513-574-8500 or contact Sur-Seal online now!
Die-Cutting Solutions for Any Industry
For more than 80 years, Sur-Seal has served dozens of industries seeking die-cut solutions for their manufacturing and production needs. Our innovative technologies have created high-quality parts for the following industries and beyond:
- Aerospace
- Appliance
- Avionics
- Buses
- Compressors
- Consumer products
- Controls and switches
- Electrical enclosures
- Elevators
- Escalators
- Government
- Health and safety
- Heavy truck
- Injection molding
- LED lighting
- Medical devices
- Military
- Power tools
- Rail
- Refrigeration
- Safety and security
- Sheet metal fabrication
- Transformers
- Turbines
- Window and door
- Aerostructures
- Automotive
- Building and construction
- Commercial vehicles
- Consumer electronics
- Contract manufacturing
- Copiers and printers
- Electronics
- Engines
- Generators
- Handheld devices
- Healthcare
- HVAC
- Lawn and garden
- Marine
- Meters
- Off-road equipment
- Pumps
- Recreational equipment
- Renewable energy
- Servers
- Telcom
- Transportation
- Valves
We can produce any shape or size you need from the materials you approve for use. Our materials include foams, rubbers, silicones, nonwovens, papers, films, foils, and more. Sur-Seal can deliver, no matter the shape, size, material, or time constraints for your project.
Call 513-574-8500 or contact us online to find out more about our industry-specific die-cutting services.
A 3M Preferred Converter
As a custom die-cutting provider, Sur-Seal is dedicated to meeting the unique needs of our clients. That is why we are a 3M Preferred Converter. By incorporating 3M’s advanced materials and adhesives into our manufacturing processes, we can provide customized solutions tailored to our clients’ needs. 3M materials help us to meet demanding manufacturing challenges to deliver a better-finished product for our customers. With over 55,000 available products, 3M has innovative solutions for almost any application.
Sur-Seal is also a 3M Preferred Automotive Converter. With quality 3M materials, we can produce a wide range of custom solutions for the automotive industry, including gaskets, seals, weatherstripping, thermal insulation products, electrical insulation, and more. Thanks to 3M materials, our products can withstand the unique challenges of the automotive environment to provide our clients with long-lasting, reliable performance.
To learn how our status as a 3M Preferred Converter helps us do more for your business, call Sur-Seal today 513-574-8500.
Choose Sur-Seal: A Top Die-Cutting Company
When you need a custom-cut solution for your business, trust the team that’s been in business for over 80 years. Our precision-cut, die-cut products are made with the highest-quality materials using advanced technologies for cost-efficient and quick production. We have AS9100 and ISO9001 certifications for expert service you can depend on every time. Contact our team to find out more about how our die-cutting solutions can bring your ideas to life.
Call 513-574-8500 or contact Sur-Seal online for custom die-cutting services.