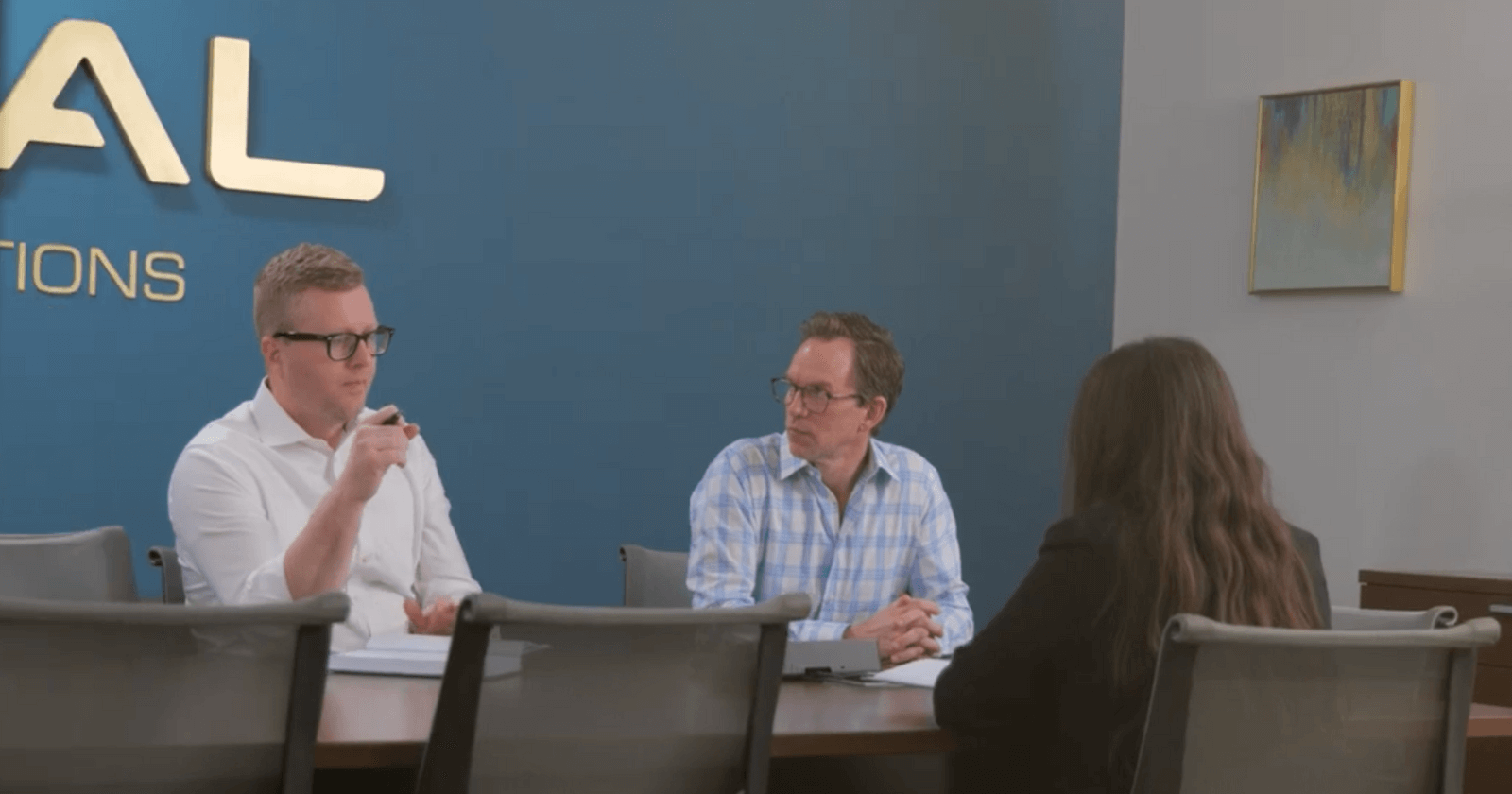
And How Sur-Seal Is Answering Them Tariff volatility isn’t just a finance problem; it’s a supply chain problem. Procurement teams...
Attention to detail is crucial when crafting electronic products. That’s why it’s crucial to select the correct type of gasket for your product, which isn’t always an easy decision to make.
When your product needs to be fine-tuned for long term use, you need to consider whether your gasket should have a high or low compression set. However, this can be difficult to do when you’re not sure what to be looking for in your gasket material.
If you’re working on a project, but you’re not sure which gasket type to use, then this is the guide for you. The experts at Sur-Seal are here to help you fully understand compression sets, gaskets, and, ultimately, how to make an informed decision for your product.
A material’s compression set, in simple terms, is the amount of permanent deformation that a product (in this case, a gasket) sustains when put under pressure or force.
Here’s an example to help clarify. If you were to put a piece of foam under your desk and leave it there for one month before removing it, the amount of indentation on the foam after removing it would be its compression set. The more indented, the higher the compression set. The less indented, the lower the compression set.
An object’s compression set can be measured and is expressed as a percentage of the permanent deformation caused by whatever force was exerted on it.
If a gasket material has a low compression set, it is suitable for products that see constant use. This is because materials with a low compression set will return to their original shape and density after being compressed, which gives them a long life span.
According to Sur-Seal industry expert Danny Davis, the best materials to use if you want a low compression set include microcellular urethane (semi open-cell foam), crushed NBR-PVC, and silicone. These soft, adaptable, and malleable materials all feature low compression sets, as well as boast some useful characteristics.
For a product that features tactile components such as a touch screen, using gaskets with low compression sets is necessary. Flexible, soft materials are perfect for products that require constant use, as they always return to their original thickness and shape. Those qualities also make foam or silicone gaskets perfect for electronic products with doors or other elements that might be opened or closed regularly.
If your gasket material is also working as a dust barrier, then microcellular urethane and crushed NBR-PVC both fit the bill exceptionally well. These two foams are both open enough to maintain a low compression set while also effectively blocking out dust and debris from your electronic devices. Crushed NBR-PVC, in particular, excels at fitting into irregular surfaces while maintaining its low compression set, making it even more versatile.
However, both microcellular urethane and crushed NBR-PVC feature very low water resistance, making them unideal for outdoor product use. If your electronic product is going to be exposed to the environment, you should use a silicone sponge gasket, which is a flexible yet stronger material than open-cell or crushed foam.
In short, gasket materials with low compression sets are generally flexible, soft, and long-lasting. These three characteristics make them perfect for tactile or movable electronic products that require medium to long life cycles.
If a material has a high compression set, it does not return to its original shape or density after being compressed, leaving the material with a permanent indentation.
Materials that have high compression sets are cross-linked (XLPE), EPDM rubber, EDA metal, PVC plastic, and neoprene blended materials. These materials all have a high compression set, as well as some practical applications in electronic products.
Gaskets with high compression sets are mostly suited for electronic products where two separate parts are attached. This means they must be made of durable, firm materials. This also means that these gaskets can be used in conjunction with adhesives.
Because these gaskets are made of inflexible material, they compress under force and their original density or shape changes. That means they will not wholly regain their original shape and end up remaining deformed. As a result, if the product that the gasket is part of is taken apart, the gasket is usually removed and replaced to ensure ongoing quality.
One major characteristic of gaskets with high compression sets is their resistance to environmental factors and contamination, which is mostly due to their material type. This means that the majority of these gasket types can be used indoors and outdoors, except for neoprene, which cannot be used outdoors due to harmful UV rays that can break the material down.
In short, gaskets that are sturdy, resistant to many forms of contamination, and are dependable, have high compression sets. These characteristics make them practical for attaching and fastening parts within electronic products.
While there are more differences than similarities between gaskets with high and low compression sets, it is still vital to highlight the differences between the two. In doing so, it will become easier to understand which gasket type is suited for any situation.
There are questions that you can ask yourself to figure out which gasket type you might need for your product. For instance, it is essential to inquire about what environment the product will be in. Will it be in a high or low-temperature area most of the time? Will it be exposed to UV rays? Is water or dust resistance something you need to consider? The answers to these questions will guide you towards what gasket you need to use.
According to Danny, considering the function of your product is vital as well. Using the incorrect type of gasket can lead to “compromising the integrity of your product,” which is to be avoided at all costs.
While gaskets with high and low compression sets may not have a lot in common, both types serve a specific and important purpose in your electronic equipment. Knowing the difference between the two is crucial.
With all this information in mind, it is now time to determine which gasket material is best for your product, starting with figuring out what level of compression set is most appropriate.
If you are looking for long-lasting, flexible gasket materials with low compression sets, then you should look to microcellular urethanes, crushed foams, or silicone sponge. These materials return to their original density use after use, as well as work to block out dust and debris from your electrical product. What they lack in resistance to the environment, they make up for in longevity.
If you are looking for strong and resistant gasket materials that have high compression sets, then you should look to neoprene, PVC, XLPE, or neoprene blend materials. These are resistant to many environmental factors that might otherwise negatively affect your product. While they might not be suited for constant delicate use, these materials are much stronger in other ways.
Essentially, the type of gasket material you choose is dependent on your product’s needs. As Danny put it, “it’s all application dependent.” When it comes time to select a gasket based upon your compression set needs for any application, use this guide to help you make the most informed decision possible.