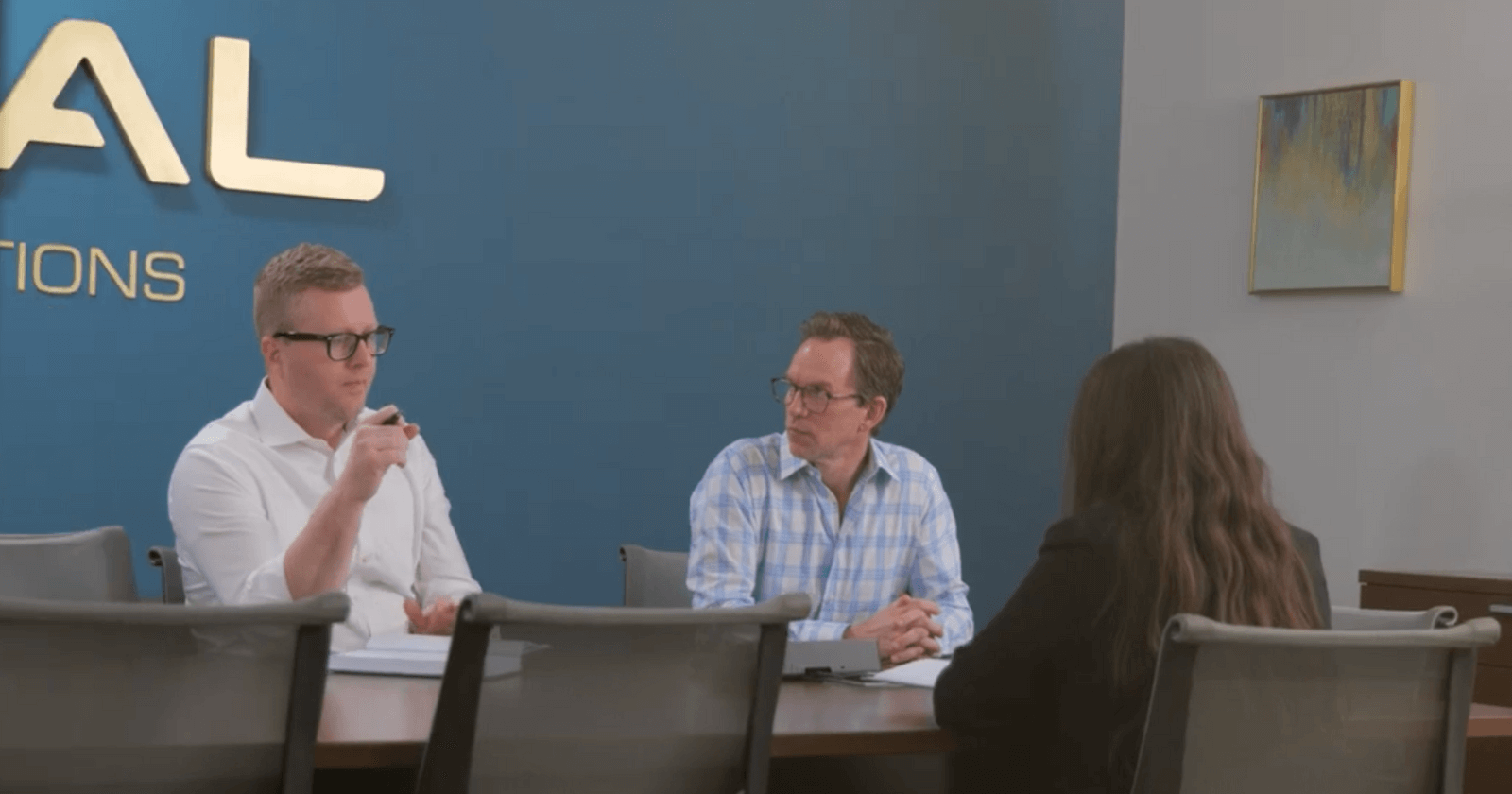
And How Sur-Seal Is Answering Them Tariff volatility isn’t just a finance problem; it’s a supply chain problem. Procurement teams...
When one of the world’s largest medical device developers presented a scenario in which they faced challenges with their medical grade tubing, Sur-Seal stood out among the crowd of potential sources. Sur-Seal offered cleanly manufactured and processed tubing to eliminate the risk of bioburden on the tubing components.
The device required several different kinds of tubing, both medical grade plastic and rubber. The performance of tubing was critical to the function of the class II medical device.
Sur-Seal went beyond the base requirement of simply supplying the tubing. Sur-Seal reduced our customer’s risk in three key ways:
- Identified better material to eliminate product issue
- Reduced potential for contamination
- Improved part traceability and addressed short shelf life
During testing, the initial PVC tubing specified had issues with blooming after Ethylene Oxide (EtO) single-use sterilization. Sur-Seal’s material experts recommended a material for the application that eliminated material blooming and potential contamination.
With the elimination of blooming during EtO sterilization, Sur-Seal helped our customer reduce risk of contamination carried within the tubes.
Ensuring the extruded tubing is utilized within its recommend shelf life proved a challenge to our client. Sur-Seal ensured the part was extruded, cut, and printed in a clean-room environment with the date of extrusion to address traceability requirements. Sur-Seal supported our client’s need for small batches to ensure all parts are freshly extruded as to not be used beyond their recommended shelf life.
Also, Sur-Seal’s Application Engineering team fine-tuned the secondary processes, including tipping and assembly of the tubing, to improve the connections between tube and tube fitting by eliminating buckling at the joints. Thermal forming techniques eliminated flow restrictions and kinking.